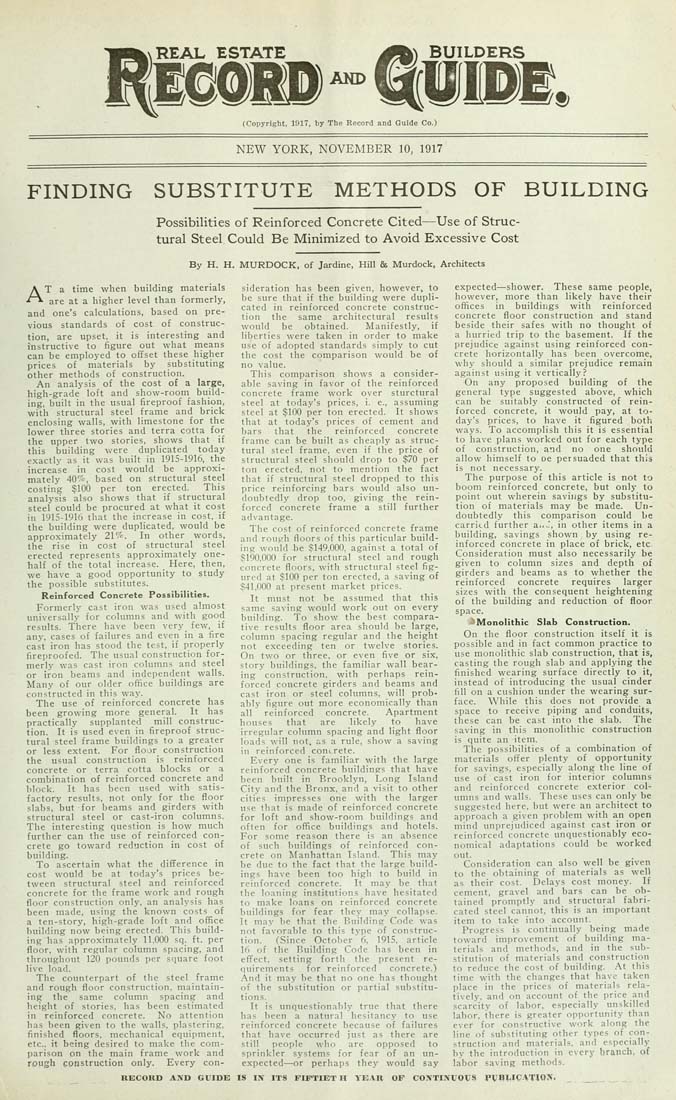
Text version:
Please note: this text may be incomplete. For more information about this OCR, view
About OCR text.
REAL ESTATE AND (Copyright, 1017, by The Record and Guide Co.) NEW YORK, NOVEMBER 10, 1917 FINDING SUBSTITUTE METHODS OF BUILDING Possibilities of Reinforced Concrete Cited—Use of Struc¬ tural Steel Could Be Minimized to Avoid Excessive Cost By H. H. MURDOCK. of Jardine, HiU Ss Murdock, Architects AT a time when building materials are at a higher level than formerly, and one's calculations, based on pre¬ vious standards of cost of construc¬ tion, are upset, it is interesting and instructive to figure out what means can be employed to offset these higher prices of materials by substituting other methods of construction. An analysis of the cost of a large, high-grade loft and show-room build¬ ing, built in the usual fireproof fashion, with structural steel frame and brick enclosing walls, with limestone for the lower three stories and terra cotta for the upper two stories, shows that if this building were duplicated today exactly as it was built in 1915-1916, the increase in cost would be approxi¬ mately 40%, based on structural steel costing $100 per ton erected. This analysis also shows that if structural steel could be procured at what it cost in 1915-1916 that the increase in cost, if the building were duplicated, would be approximately 21%. In other words, the rise in cost of structural steel erected represents approximately one- half of the total increase. _ Here, then, we have a good opportunity to study the possible substitutes. Reinforced Concrete Possibilities. Formerly cast iron was used almost universally for columns and with good results. There have been very^ few, if any, cases of failures and even in a fire cast iron has stood the test, if properly fireproofed. The usual construction for¬ merly was cast iron columns and steel or iron beams and independent walls. Many of our older office buildings are constructed in this way. The use of reinforced concrete has been growing more general. It has practically supplanted mill construc¬ tion. It is used even in fireproof struc¬ tural steel frame buildings to a greater or less extent. For floor construction the usual construction is reinforced concrete or terra cotta blocks or a combination of reinforced concrete and block. It has been used with satis¬ factory results, not only for the floor slabs, but for beams and girders with structural steel or cast-iron columns. The interesting question is how much further can the use of reinforced con¬ crete go toward reduction in cost of building. To ascertain what the difference in cost would be at today's prices be¬ tween structural steel and reinforced concrete for the frame work and rough floor construction only, an analysis has been made, using the known costs of a ten-story, high-grade loft and office building now being erected. This build¬ ing has approximately 11,000 sq. ft. per floor, with regular column spacing, and throughout 120 pounds per square foot live load. The counterpart of the steel frame and rough floor construction, maintain¬ ing the same column spacing and height of stories, has been estimated in reinforced concrete. No attention has been given to the walls, plastering, finished floors, mechanical equipment, etc.. it being desired to make the com¬ parison on the main frame work and rough construction only. Every con¬ sideration has been given, however^ to be sure that if the building were dupli¬ cated in reinforced concrete construc¬ tion the same architectural results would be obtained. Manifestly, if liberties were taken in order to make use of adopted standards simply to cut the cost the comparison would be of no value. This comparison shows a consider¬ able saving in favor of the reinforced concrete frame work over sturctural steel at today's prices, i. e., assuming steel at $100 per ton erected. It shows that at today's prices of cement and bars that the reinforced concrete frame can be built as cheaply as struc¬ tural steel frame, even if the price of structural steel should drop to $70 per ton erected, not to mention the fact that if structural steel dropped to this price reinforcing bars would also un¬ doubtedly drop too, giving the rein¬ forced concrete frame a still further advantage. The cost of reinforced concrete frame and rough floors of this particular build- in.e: would be $149,000, against a total of $190,000 for structural steel and rough concrete floors, with structural steel fig¬ ured at $100 per ton erected, a saving of $41,000 at present market prices. It must not be assumed that this same saving would work out on every building. To show the best compara¬ tive results floor area should be large, column spacing regular and the height not exceeding ten or twelve stories. On two or three, or even five or six, story buildings, the familiar wall bear¬ ing construction, with perhaps rein¬ forced concrete girders and beams and cast iron or steel columns, will prob¬ ably figure out more economically than all reinforced concrete. Apartment houses that are likely to have irregular column spacing and light floor loads will not» as a rule, show a saving in reinforced concrete. Every one is familiar with the large reinforced concrete buildings that have been built in Brooklyn, Long Island City and the Bronx, and a visit to other cities impresses one with the larger use that is made of reinforced concrete for loft and show-room buildings and often for office buildings and hotels. For some reason there is an absence of such buildings of reinforced con¬ crete on Manhattan Island. This may be due to the fact that the large build¬ ings have been too high to build in reinforced concrete. It may be that the loaning institutions have hesitated to make loans on reinforced concrete buildings for fear they may collapse. It may be that the Building Code was not favorable to this type of construc¬ tion. (Since October 6, 1915, article 16 of the Building Code has been in effect, setting forth the present re¬ quirements for reinforced concrete.) And it may be that no one has thought of the substitution or partial substitu¬ tions. It is unquestionably true that there has been a natural hesitancy to use reinforced concrete because of failures that have occurred just as there are still people who are opposed to sprinkler systems for fear of an un¬ expected—or perhaps they would say expected—shower. These same people, however, more than likely have their offices in buildings with reinforced concrete floor construction and stand beside their safes with no thought of a hurried trip to the basement. If the prejudice against using reinforced con¬ crete horizontally has been overcome, why should a similar prejudice remain against using it vertically? On any proposed building of the general type suggested above, which can be suitably constructed of rein¬ forced concrete, it would pay, at to¬ day's prices, to have it figured both ways. To accomplish this it is essential to have plans worked out for each type of construction, and no one should allow himself to oe persuaded that this is not necessary. The purpose of this article is not to boom reinforced concrete, but only to point out wherein savings by substitu¬ tion of materials may be made. Un¬ doubtedly this comparison could be carried further ai.^, in other items in a building, savings shown by using re¬ inforced concrete in place of brick, etc Consideration must also necessarily be given to column sizes and depth of girders and beams as to whether the reinforced concrete requires larger sizes with the consequent heightening of the building and reduction of floor space. ^Monolithic Slab Construction. On the floor construction itself it is possible and in fact common practice to use monolithic slab construction, that is, casting the rough slab and applying the finished wearing surface directly to it, instead of introducing the usual cinder fill on a cushion under the wearing sur¬ face. While this does not provide_ a space to receive piping and conduits, these can be cast into the slab. The saving in this monolithic construction is quite an item. The possibilities of a combination of materials offer plenty of opportunity for savings, especially along the line of use of cast iron for interior columns and reinforced concrete exterior col¬ umns and walls. These uses can only be suggested here, but were an architect to approach a given problem with an open mind unprejudiced against cast iron or reinforced concrete unquestionably eco¬ nomical adaptations could be worked out. Consideration can also well be given to the obtaining of materials as well as their cost. Delays cost money. If cement, gravel and bars can be ob¬ tained promptly and structural fabri¬ cated steel cannot, this is an important item to take into account. Progress is continually being made toward improvement of building ma¬ terials and methods, and in the sub¬ stitution of materials and construction to reduce the cost of building. At this time with the changes that have taken place in the prices of materials rela¬ tively, and on account of the price and scarcity of labor, especially unskilled labor, there is greater opportunity than ever for constructive work along the line of substituting other types of con¬ struction and materials, and especially by the introduction in every branch, of labor saving methods. RBCORD AND GUIDE IS IN ITS FIFTIETH YEAR OF CONTINUOUS PUBLICATION.